Prevent Scaling on Gate Valves: Top Coating Solutions for Longevity
Discover effective coatings to prevent scaling in gate valves, enhancing their longevity and performance.
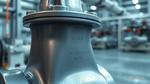
Understanding Scaling in Gate Valves
Let’s dive into scaling. What is it, anyway? Scaling refers to the buildup of minerals, like calcium and magnesium, that forms a hard layer on the surfaces of gate valves. This pesky issue often happens when water or other liquids carry these minerals. When the fluids flow through the valve, they can settle on the valve surfaces, hardening over time. Think of it like how limescale builds up in your kettle or coffee maker. Annoying, right?
Now, why is it crucial to prevent scaling? Well, scaling might not seem like a big deal at first, but trust me, it can wreak havoc. If you ignore it, this buildup can obstruct the flow of liquids. This not only leads to reduced efficiency but can also result in increased energy costs. Plus, let’s not forget the potential for costly repairs down the line. A bit of foresight in scaling prevention can save a world of headaches!
What about the effects of scaling on valve performance? It’s pretty straightforward. Valves that have a thick buildup of scale can become harder to operate. They might not seal as tightly, which can lead to leaks. This can cause not only wasted resources but also potential safety hazards. With aging infrastructure, it can create catastrophic failures if left unchecked—a bit like ignoring that small leak in your roof until it becomes a serious issue.
So, if you're wondering how to tackle this dilemma, one effective way to prevent scaling on gate valves by coating is using protective coatings. These coatings can create a barrier, reducing mineral attachment. Plus, they often come with added benefits, like resistance to corrosion and improved longevity. Just think of it as a shield for your gate valve—a smart choice for smooth, efficient operation. With a little bit of effort and some clever coatings, you can keep those valves running like new, dodging the dreaded scaling issue!
Common Causes of Scaling
Scaling can be a real thorn in the side when dealing with gate valves. It’s like that stubborn stain that just won’t budge. Let’s take a stroll through the common culprits behind scaling, shall we?
Water Quality and Its Impact
First off, the quality of water plays a massive role. If the water is hard, it’s packed with minerals like calcium and magnesium. Think of it as Mother Nature's way of giving your plumbing a workout. Over time, those minerals build up, creating a crusty layer. This isn’t just bad for the flow—it can really mess with the valve’s function.
If you want to keep your gate valves in tip-top shape, regular checks on water quality can prevent scaling on gate valves by coating. It’s all about being proactive. And trust me, staying ahead of the game beats dealing with a jammed valve later.
Temperature Variations
Now, let’s chat about temperature. Those swings—like the weather in April—can lead to scaling too. When temperatures fluctuate, it can cause the minerals in the water to either dissolve or precipitate out, forming those pesky deposits. Picture a hot cup of coffee that leaves a ring; it’s a similar deal inside your pipes.
To avoid the startup blues every season, keeping your system at a steady temperature can help. Think of it as a cozy blanket for your piping. If you can manage it, you’ll see fewer headaches down the line.
Chemical Reactions in Industrial Applications
Lastly, let’s touch on chemical reactions, especially in industrial setups. Sometimes, the very processes meant to help can contribute to scaling. Chemicals used for cleaning or reactions in production might mix weirdly with water, giving rise to that unwanted scaling. It’s like baking—too much of one ingredient can spoil the whole batch.
Being aware of what chemicals are floating around in your system can make a huge difference. Regular maintenance and monitoring can save time and money. Always best to catch it early than find yourself scrubbing away on a Saturday.
So, remember—keeping an eye on water quality, managing those temperature changes, and being wary of chemical interactions are all key steps. It’s about laying down a solid game plan to prevent scaling on gate valves by coating. With that kind of foresight, your valves should stay in great shape, ready to do their job without fuss!
Advantages of Using Coatings
When it comes to keeping gate valves in tip-top shape, coatings are like a knight’s armor—ready to battle the elements! Let’s dive into some reasons why using coatings can be a game-changer, especially when you want to prevent scaling on gate valves by coating.
Enhanced Corrosion Resistance
First off, let’s talk about corrosion. Nobody wants to deal with that rust monster creeping in, right? Coatings provide an extra layer that helps fend off moisture and chemicals. It’s like putting a shield between the valve and the nasty stuff that can cause wear and tear. You’ll find that valves with good coatings resist corrosion much better, keeping them strong for years to come. It’s amazing how a simple coat can make such a difference!
Improved Longevity of Valves
Now, who doesn’t want their valves to have a longer life? With proper coatings, you can extend their lifespan significantly. Think of it as giving them a little extra TLC. You know how some folks swear by certain oils to keep their cars running smoothly? Well, coatings do a similar job. They prevent the harsh elements from doing their worst. So, not only do your valves last longer, but you'll also save yourself some headaches down the road.
Cost-Effectiveness of Preventive Measures
Let’s not sugarcoat it—maintenance can be pricey. But when you prevent scaling on gate valves by coating them, you’re actually saving money in the long run. Think of it like investing in a good pair of boots. You might spend a bit more upfront, but they’ll last longer and keep your feet dry. Coatings help you avoid costly replacements and repairs. Plus, who wouldn’t want to spend less and get more?
When you weigh the pros and cons, it’s clear that using coatings is a smart choice. It’s a straightforward way to keep your gate valves in great shape. So, next time you’re considering how to battle corrosion and extend the life of your valves, remember that a good coating might just be your best ally.
Types of Coatings for Valve Protection
Alright, let’s dive into the world of coatings for valve protection. If you’re wondering how to prevent scaling on gate valves by coating, you’re in the right spot. We'll break it down into bite-sized pieces, easy as pie.
Overview of Protective Coating Options
When it comes to protecting those trusty gate valves, there’s a whole toolbox of coatings to choose from. Think of coatings as a knight’s armor — they’re here to safeguard our valves from the nasty stuff, like corrosion and scaling. You’ve got options like epoxy, polyurethane, and fluoropolymer. Each one has its strengths and weaknesses. Just like picking ale, it all comes down to what works best for your needs!
Solvent-Based vs. Water-Based Coatings
Now, let's have a chinwag about solvent-based and water-based coatings. Solvent-based coatings pack a bit more punch with their durability. They can handle high temperatures and tough environments like a champion. But here’s the catch: they might carry some fumes that make you feel like you’ve walked into a smokehouse. So, a little ventilation is a must when applying them.
On the flip side, water-based coatings are often easier on the nose — no need for a gas mask! They dry quicker and are generally more pleasant to work with. However, might not offer the same heavy-duty protection. It’s like choosing between a nice brew at the local pub or something stronger to get the job done when the going gets tough. Either choice has its time and place!
Specialty Coatings for High-Pressure Valves
If you’re dealing with high-pressure valves, then specialty coatings come into play. These coatings are like the elite guards of your valve army, designed to take on extreme conditions. For example, ceramic coatings can withstand high temperatures and pressure. They create a tough barrier that keeps scaling and corrosion at bay.
You'll want to think about what you need for your application. Sometimes, it’s about balancing cost and performance. Other times, you might just need that extra boost of protection. So, don’t be afraid to ask a few more questions or dig a little deeper into the options.
In the end, choosing the right coating is key to keeping those gate valves healthy. Prevent scaling on gate valves by coating, and you’ll save yourself a lot of headaches. Trust me, that’s a lesson learned through trial and error!
Application Techniques for Coatings
When you're looking to prevent scaling on gate valves by coating, there are a few steps to follow. Getting the coating on right is crucial to keep those pesky mineral deposits at bay. So let’s break this down bit by bit.
Pre-Coat Preparation Steps
First things first—always start with a clean slate. I mean, who wants to paint over dirt? Cleaning the surface is like getting rid of clutter before throwing a party; it sets the mood. Use a good degreaser to wipe off any grease or grime. Next, you’ll want to inspect for any rust or damage. If you find any, patch it up. A little care here goes a long way.
Then, you should roughen the surface. Sanding it lightly will give the coating something to grip onto. Think of it like velcro; the rougher it is, the better it sticks. And don’t forget to wipe it down one last time to get rid of dust—trust me, it makes a big difference.
Coating Application Methods
Now that you’ve done all that hard work, it’s time to apply the coating. There are a couple of methods you can choose from, depending on your setup and comfort level.
-
Brush Application : This is the classic way. Grab a brush and go to town. It’s easy to control and great for those hard-to-reach spots. Just make sure you get an even coat. No one likes a splotchy surface.
-
Spray Application : If you’ve got a larger area to cover, consider using a spray gun. It's quick and efficient, but you need to wear some protective gear. You wouldn't want to breathe in those fumes. Plus, you’ve got to practice a bit—nobody wants a paint-over-spray situation ruining your hard work.
-
Dip Coating : This method involves dipping the valve into the coating solution. It offers full coverage but can be overkill for smaller jobs. Still, if you’re after that perfect layer, this one’s a solid option.
Essential Coating Application Machinery
Now, let’s chat about some tools you'll need for proper application. Even if you’ve got golden hands, a little machinery goes a long way.
-
Pressure Spray Gun : This nifty piece of machinery makes it easier to apply the coating evenly. You can even adjust the pressure, which is a huge plus—less chance of drips and runs.
-
Air Compressor : If you’re going the spray route, an air compressor is pretty much essential. It helps keep everything moving and ensures that your spray gun works like a charm.
-
Mixing Equipment : Always mix your coating as per the instructions. Clumps? Not on my watch! A good mixing tool will save you from a lot of headaches later.
So, when you’re gearing up to prevent scaling on gate valves by coating, remember these steps. With the right pre-coat prep, application methods, and tools, you'll set yourself up for success. No more scaling—just smooth sailing!
Maintenance Tips for Coated Gate Valves
When it comes to keeping those coated gate valves in tip-top shape, regular maintenance is key. You wouldn’t ignore a leaky roof or a worn-out pair of boots, right? Same goes for these valves! Let’s dive into some handy tips that'll help you prevent scaling on gate valves by coating.
Regular Inspection Guidelines
First off, make it a habit to inspect your valves every few months. Grab a flashlight and look for signs of wear, rust, or any scaling. If you see any buildup, that’s an indicator that the coating might be wearing thin. A couple of minutes of inspection can save you a heap of trouble down the line. Check the seals too — if they’re cracked or worn, it’s time for a replacement. Trust me, don’t ignore it!
Recommended Maintenance Schedule
Now, onto the schedule. You don’t need to be doing this daily, but set up a routine. Checking your coated gate valves every six months is a solid plan. Start by cleaning them with a soft cloth to remove any surface grime. If you notice scaling, it might be worth reapplying the coating. That’s like putting a fresh coat of paint on your house — keeps everything looking good and functioning well. Also, consider flushing the system to clear out any debris. A little effort goes a long way!
Troubleshooting Common Issues
So, what if you run into problems? Let’s say you’re noticing leaks. First thing, check those seals. Are they snug? If not, that’s your culprit. You might also have a valve that won’t fully open or close. Give it a good wiggle and see if it’s stuck. If cleaning doesn't do the trick, you might need a new gasket or even a new valve altogether. Often, folks overlook the simplest fixes. Don’t be one of them — clean, inspect, and if you're scratching your head, don't hesitate to ask a professional.
Accidents happen. Just keep an eye on your equipment and wear and tear. With a little attention and these maintenance tips, you can prevent scaling on gate valves by coating effectively. And honestly, you’ll be glad you took the time — nobody wants to deal with valve drama, right?
Conclusion: The Importance of Preventing Scaling Using Coatings
Let’s wrap it all up, shall we? You’ve learned that scaling on gate valves can be a pesky problem. And honestly, no one wants a valve that won’t budge when you need it most. It can cause leaks, inefficient performance, and ultimately, costly repairs. Not good, right? By applying coatings, you can effectively prevent scaling on gate valves by coating. These layers not only help keep things running smoothly but also extend the life of your valves. It’s like putting on a good pair of boots before heading out into the muck—you’re prepared!
Now, here’s the quick rundown of what we covered: First off, scaling is caused by minerals and other deposits that build up over time. Big surprise, right? Secondly, coatings serve as a barrier, protecting the metal beneath. They help in reducing that build-up and maintain efficiency. Choose the right coating type to fit your needs, whether that’s a polymer-based layer or something more durable.
But don’t just take my word for it! Get out there and check on those gate valves. Regular maintenance not only saves you a headache down the line, but it also keeps everything in tip-top shape. Keep an eye out for any signs of wear, and don’t hesitate to reach out to a professional if you’re unsure.
So, here’s a friendly nudge: Look after your valves! If you want to really keep them in good condition, start thinking about how to prevent scaling on gate valves by coating them. Trust me, your future self will thank you. Take that first step today. Inspect those valves and consider the right coatings. Invest a little time now, and you won’t have to worry later!
Previous article: All About Neal Smead and His Impact
Next article: Funding Opportunities with Anthony Zingarelli 2025
Prevent Scaling on Gate Valves: Top Coating Solutions for Longevity: Share, Rating and Comments
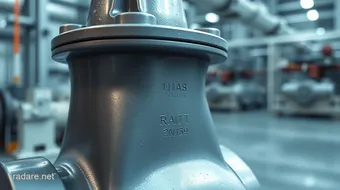
0.0 / 5
0 Review